Optimizing Quality Management With NetSuite QMS
- haniffa7
- Mar 25, 2022
- 2 min read
In order to fulfil external compliance standards and maintain the lifeblood of profitability and customer satisfaction, confirming that vendors and internal manufacturing operations achieve the quality standards is considered crucial. Manufactures from across the fields—especially medical companies have historically maintained separate quality management systems outside of their day-to-day ERP systems, which leads them to delays, lack of visibility, and process gridlocks.
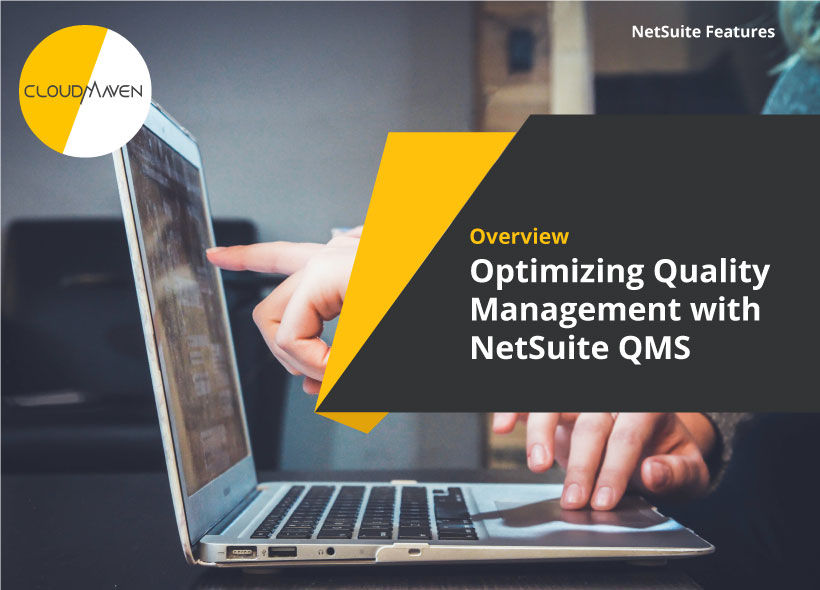
Fortunately, NetSuite offers a fully integrated Quality Management Solution that is flexible, allows for automation of pre-inspection quarantine and subsequent release of inspection-compliant material, and the ability to generate wide-ranging reporting metrics.
Flexibility
causeWith reusable inspections, users can create a single version of each inspection and group them into specifications assigned to many materials. They can also specify global standards for each inspection or create material-specific standards. Sampling and Skip Lot functionality allow for flexible inspection frequencies and data counts, and users can also specify allowable failures, if any. Be aware that sometimes too much flexibility can cause inefficient setup, so be sure to find the right NetSuite expert that takes time to understand your business and understands some of the flexibility pitfalls.
Automation
This is perhaps the most considerable benefit of QMS integration with NetSuite. The system can auto-trigger inspections based on inspection frequencies and bring them into a queue for their quality manager to assign to their quality engineers. Upon receipt of materials from vendors, workflows can systematically ‘quarantine’ material that NetSuite recognizes and disallows from commitment to work orders or customer sales orders. The workflows can also move material back to ‘good’ usable inventory upon satisfactory completion of an inspection, or even auto-trigger a return authorization back to the vendor with a failed product inspection.
Reporting Quality
Reporting Quality is all about capturing data and transforming that data into meaningful reporting for decision making. Creating an incoming inspection scorecard, vendor scorecard, and a production specification scorecard combined with Lot Traceability will ensure managers have real-time notifications when a quality issue occurs and can react accordingly. These endlessly flexible reports allow quality managers to continually monitor quality trends in real-time before quality issues become too costly.
NetSuite is still rolling out new Quality Management improvements with each release so now is the time to look at this great software solution. Talk to your NetSuite consultant about whether NetSuite Quality Management is a good fit for your organization.
Whether you are looking for a one-stop-shop for all CloudERP service, or simply need answers to your questions, our experts are here to make your business better. Cloudmaven is only one call away to make your whole easy ERP journey comes true.
Comments